L’attrito, o più correttamente la forza di attrito, è l’avversario più temibile di tutti gli ingranaggi, sia rotativi, sia a leva. Cominciamo ad esaminarne le caratteristiche, gli effetti e le risoluzioni.
L’ esistenza di questa forza era nota fin dall’antichità. Aristotele nei suoi studi dichiarava : “Un corpo tende a fermarsi naturalmente se non è mosso da una forza qualunque.“ La difficoltà che incontrano due materiali a scivolare tra loro viene indicata con il coefficiente d’attrito, mentre la forza verticale è detta carico. L’ attrito risulta essere la somma tra il coefficiente ed il carico e il suo effetto è la dissipazione (perdita) di energia e l’usura delle parti coinvolte. Si distinguono varie tipologie di attrito: il Radente (statico e dinamico), il Volvente ed il Viscoso. Tutte producono, comunque, degli effetti negativi nei congegni meccanici ed ovviamente anche l’orologio non ne viene risparmiato.
La soluzione si trova nel Lubrificante. Sotto forma di olio o grasso, questa sostanza interposta tra le parti in contatto crea un sottilissimo velo incomprimibile che contrasta temporaneamente l’attrito; infatti, i lubrificanti hanno una durata ben precisa che varia sia per la natura della loro composizione, che per la l’intensità degli attriti che debbono contrastare. Periodicamente, le caratteristiche di tali sostanze, Viscosità e Densità, che permettono lo scorrimento degli ingranaggi, si attenuano e si rende necessario il lavaggio dei residui e l’applicazione di una nuova quantità.
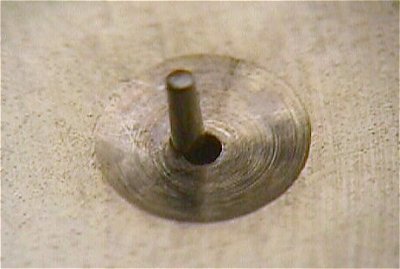
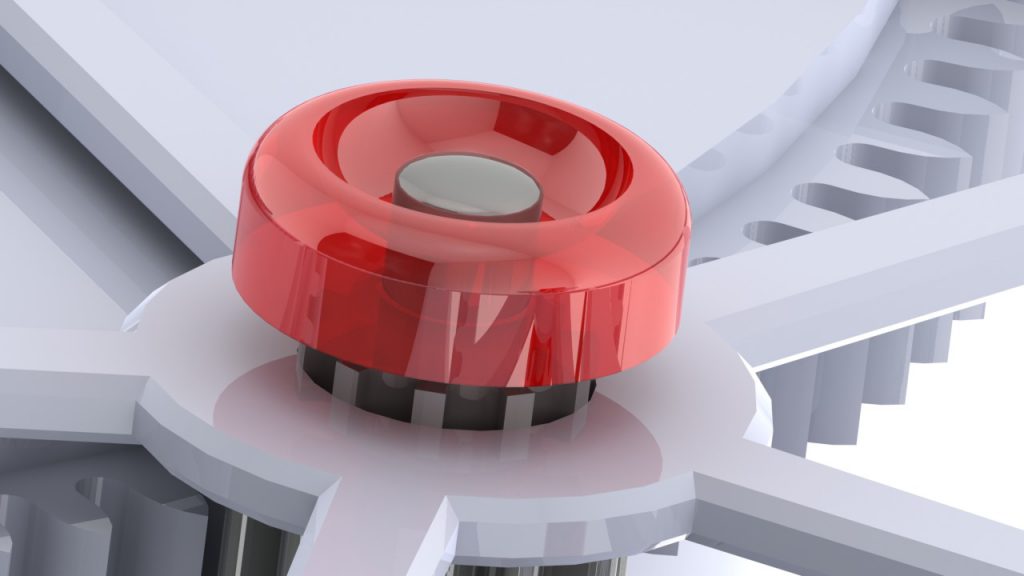
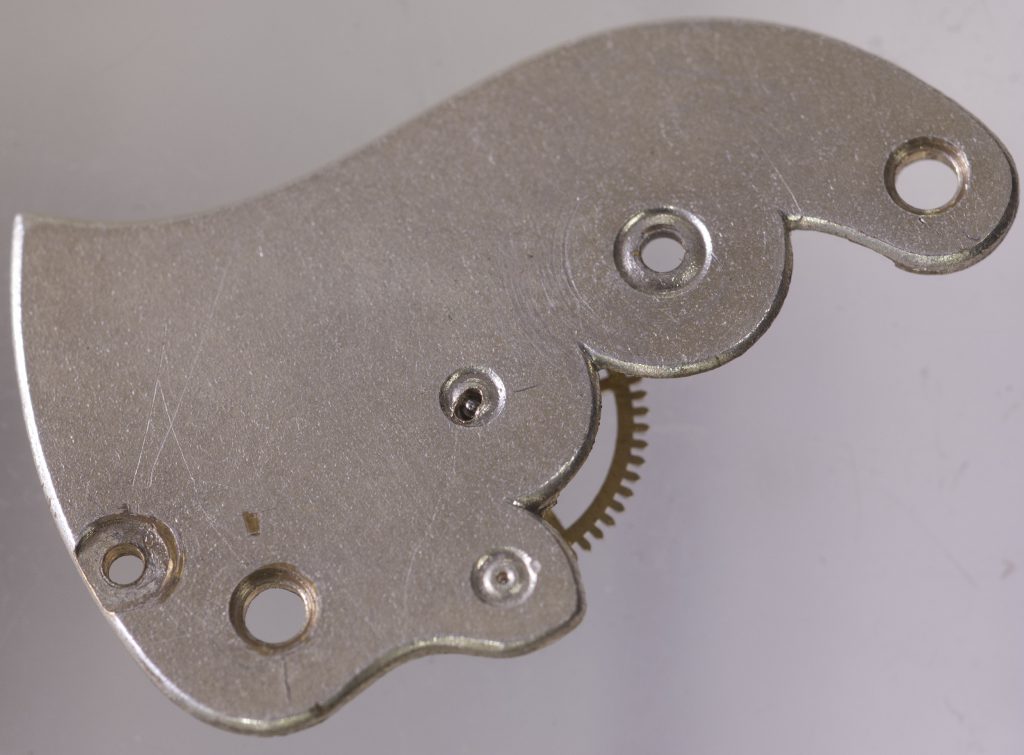
Nei primi orologi, i perni di rotazione delle ruote, in acciaio, giravano liberamente all’interno dei fori praticati nella platina e nei ponti, costruiti invece in ottone: ovviamente, le durezze meccaniche che presentano i due materiali sono molto diverse. La pressione laterale esercitata sul perno dal sistema “molla/bariletto”, abbinata alla rotazione impressa alla ruota da quest’ultimo, consumano inizialmente la sede (foro) in maniera non regolare (tipo alesaggio), ma fuori centro, creando così un nuovo alloggiamento con la classica forma ad “8”. Più lentamente, anche il perno subisce un inevitabile danneggiamento e il risultato finale è facilmente intuibile: la ruota, oltre a perdere il gioco assiale non lavora più in linea con il proprio asse e la dentatura di conseguenza non ingrana con le ali del pignone seguente rispettando un’angolazione di 90°; il profilo del dente, a questo punto, si deforma compromettendo tutto il corretto funzionamento dell’orologio.
Nicolas Fatio de Duillier, matematico svizzero, nel 1689, trovò il rimedio definitivo, inventando un procedimento per l’impiego delle pietre preziose forate. Infatti, anche se opportunamente aggiornato e migliorato negli anni sulla scia dell’evoluzione tecnologica, il principio di base non è stato, ad oggi, modificato. Si tratta dell’introduzione del rubino: la pietra di proporzioni minute veniva sagomata e forata con estrema abilità, tenendo conto degli strumenti di cui disponevano all’epoca gli artigiani. L’idea fu di inserire un materiale più duro tra i perni delle ruote e la loro sede di rotazione. Si veniva così a creare un cuscinetto a strisciamento, che sosteneva e guidava il perno, consentendone un’accurata lubrificazione tramite un apposita svasatura ricavata al suo interno. Di fatto, l’olio viene dosato nel rubino con degli utensili dedicati chiamati “oliatori”: costruiti in misure assortite, raccolgono la giusta quantità di lubrificante in relazione alla dimensione della pietra e del carico che la ruota deve sostenere.
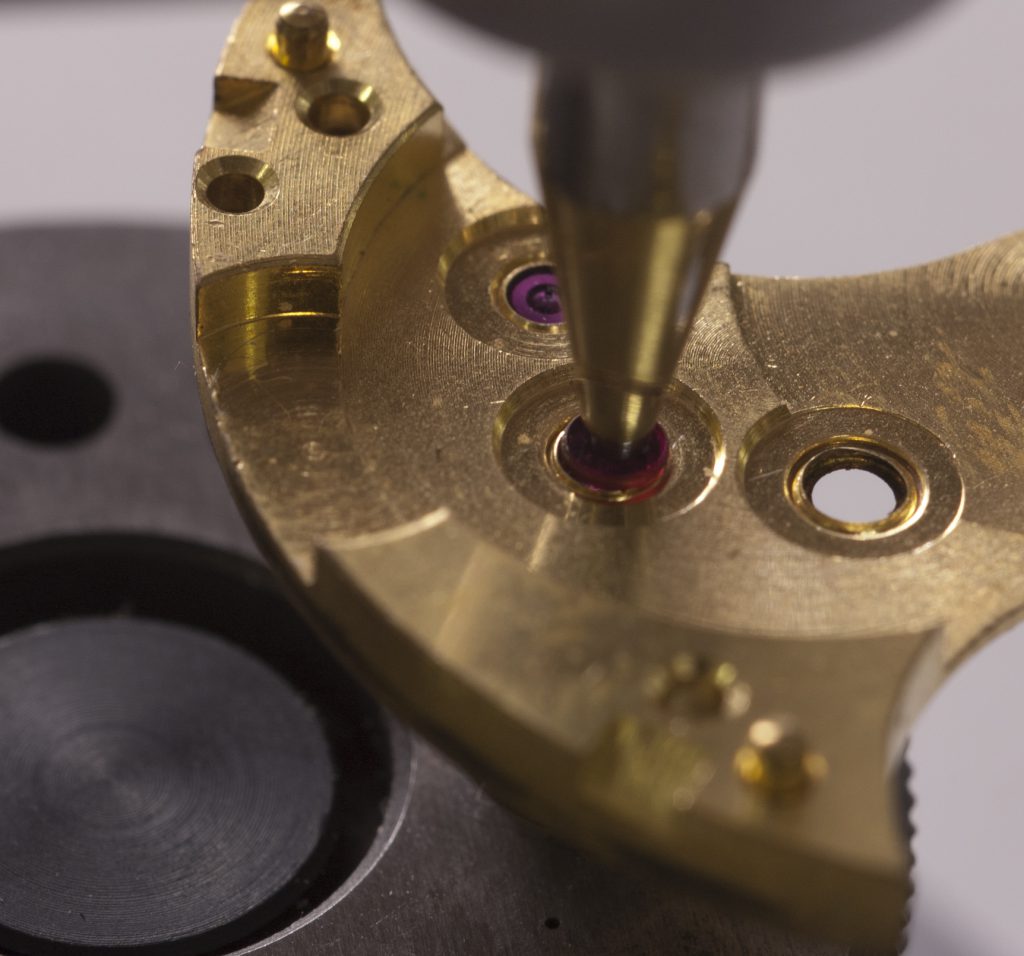
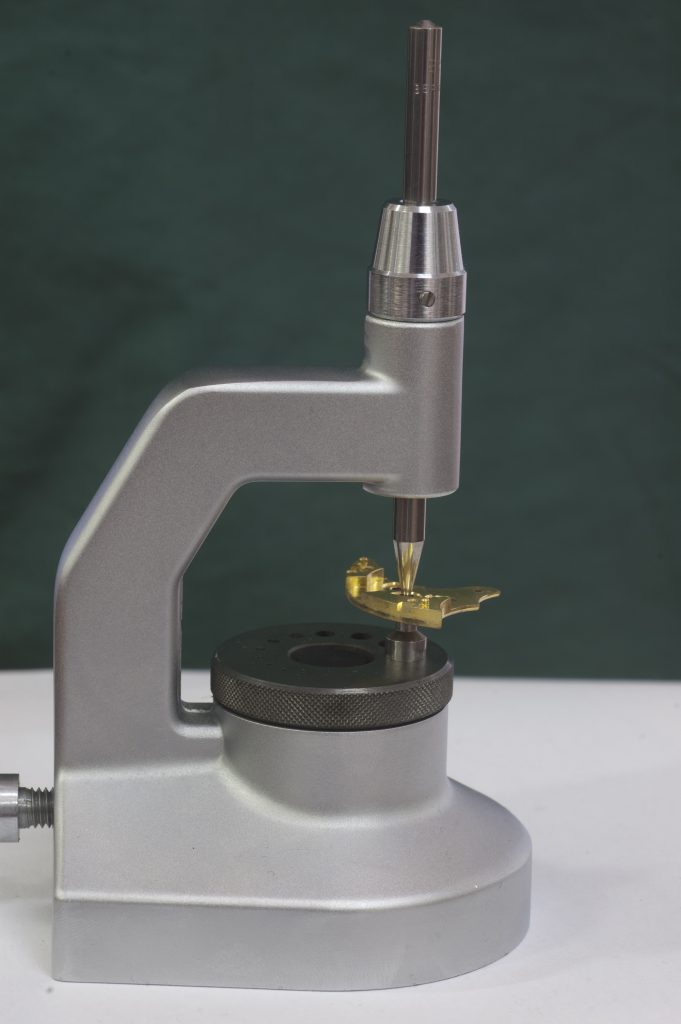
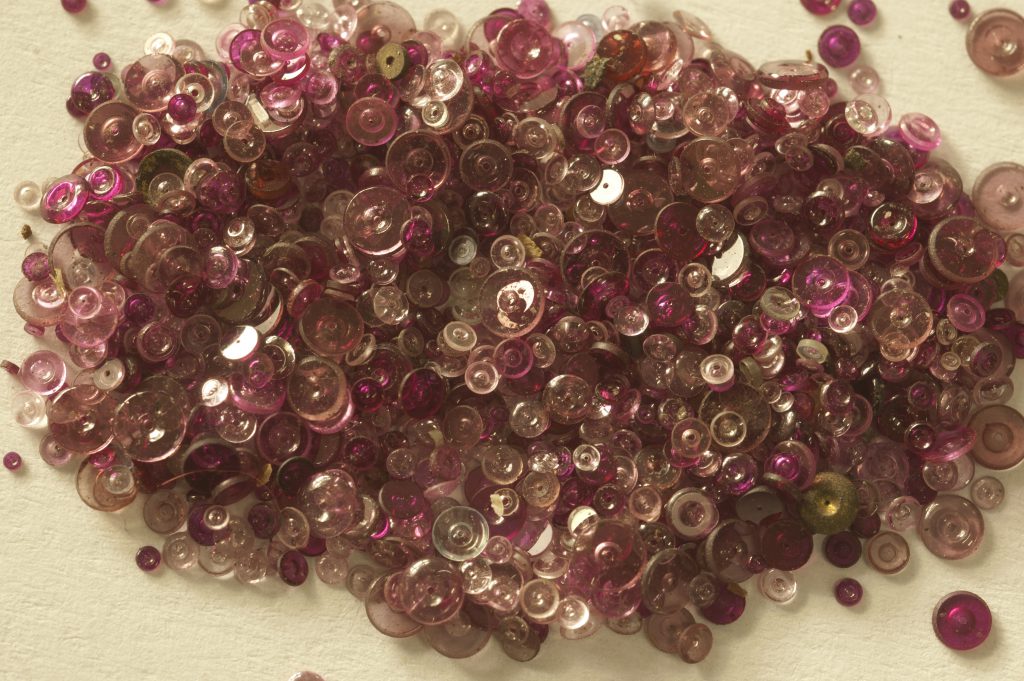
Perché la scelta del rubino? Nella sua semplicità, è il componente all’interno del meccanismo che più ha sollecitato ed alimentato la fantasia dei possessori di un orologio; storie divenute vere e proprie leggende metropolitane, riguardo a sostituzioni e sparizioni effettuate da orologiai più simili ad un Arsenio Lupin, che ad un vero tecnico che ne conosce la reale natura ed il suo concreto valore.
La durezza del rubino è inferiore solo a quella del diamante, che, quindi, si utilizza nelle fasi di lavorazione. Inizialmente, le pietre erano naturali e l’impiego si limitava ad orologi molto importanti e prestigiosi, ma alla fine del 1800, il chimico francese Auguste Verneuil mise a punto un procedimento per la produzione di corindoni (rubini) sintetici, rivoluzionando il mondo dell’orologeria: il basso costo di produzione, abbinato con l’alta qualità del risultato ottenuto, consentiva il montaggio delle pietre praticamente in ogni meccanica e solamente i calibri veramente economici non ne usufruivano. Il suddetto processo, denominato Verneuil, avveniva in un forno speciale, di sua progettazione, alimentato da una fiamma a idrogeno e ossigeno che, raggiunti i 2.200° C, sinterizzava (trasformazione in un composto indivisibile) una finissima polvere composta da ossido di alluminio (allumina), a cui l’aggiunta di cromo conferiva il colore rosso. La polvere sinterizzata così ottenuta, veniva fatta cadere lentamente dall’alto su di un supporto, creando così un effetto “stalagmite”. La somma dei vari strati formava una boule, che una volta raffreddata, presentava tutte le caratteristiche tecniche del rubino, ma non certo il suo elevato valore economico. Nel 1886, l’industriale Giovanni Sinigaglia impiantò, nella zona del Cremonese, una fabbrica per la realizzazione di rubini per orologeria, attività che si svilupperà rapidamente in tutta la zona, con diversi centri di produzione specializzati in operazioni di meccanica di precisione. Tale iniziativa continuerà per quasi un secolo, “sfornando” milioni di corindoni sintetici che montati nei maggiori punti d’attrito, avevano e hanno il compito di migliorare la precisione dei nostri orologi.
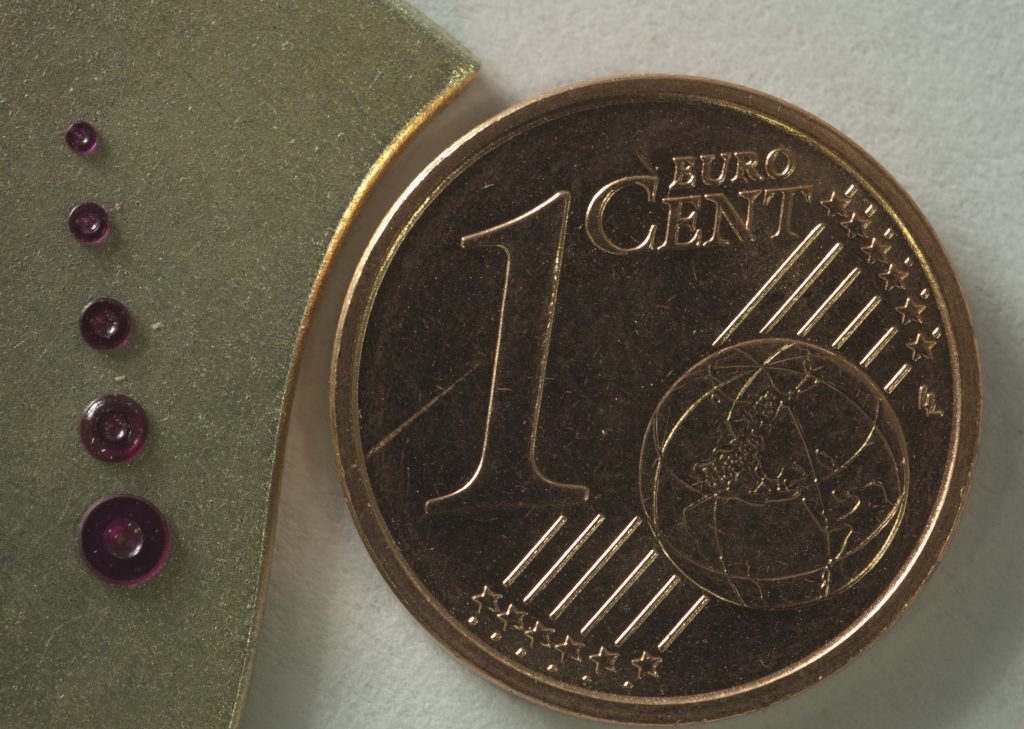
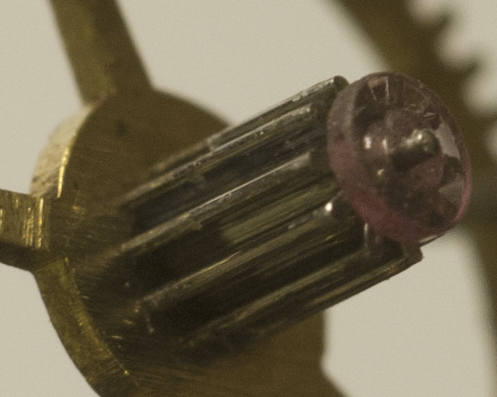
Il rubino, a motivo del suo più comune sistema di montaggio, viene indicato anche con il termine di pietra a forzamento o a pressione: infatti, il suo posizionamento, da parte dell’orologiaio, avviene tramite un utensile tipico di quest’arte, denominato punzoniera. Si tratta di un attrezzo in uso fin dagli albori dell’orologeria: un’ingegnosa, piccola struttura fa da sostegno e guida ad un punzone che, percosso da un apposito martelletto, si muoverà perfettamente sulla sua verticale permettendo così un lavoro di estrema precisione. La pietra, con un diametro leggermente superiore alla sede di montaggio, viene “forzata” al suo interno, bloccandosi saldamente. Inoltre, il tecnico determinerà anche la profondità d’inserimento in modo da conferire il giusto gioco assiale all’ingranaggio. Oltre a svolgere il compito di cuscinetto, il rubino viene anche utilizzato nella costruzione dei sistemi antiurto per gli assi del bilanciere: tale dispositivo, ormai in uso in tutte le meccaniche, svolge un’ azione di ammortizzatore, proteggendo l’asse, entro certi limiti, da colpi e sobbalzi. Approfondiremo tale tema, nel prossimo appuntamento tecnico.
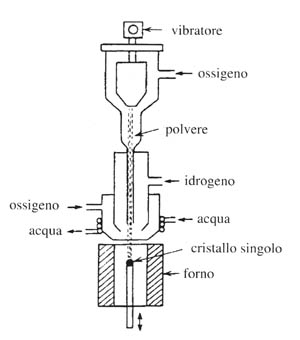
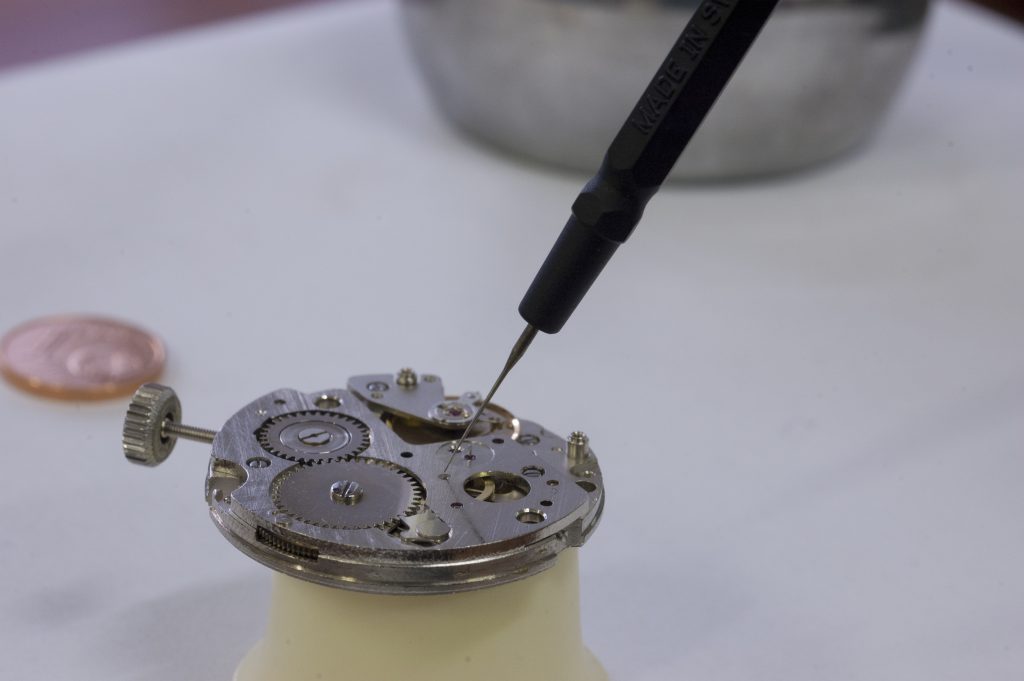
Da circa 25 anni, giornalista specializzato in orologeria, ha lavorato per i più importanti magazine nazionali del settore con ruoli di responsabilità. Freelance, oggi è Watch Editor de Il Giornale e Vice Direttore di Revolution Italia
Nessun commento